Pourquoi choisir les offres d'oxycombustion d'Air Liquide pour l'acier, la fonte ou les métaux non ferreux?
|
Économies d'énergieL'utilisation d'oxygène pur au lieu de l'air améliore l'efficacité de la combustion et réduit la consommation de combustible. En remplaçant l'air par de l'oxygène, vous économisez de l'énergie tout en réduisant le volume des gaz de combustion, car il n'y a pas d'azote à chauffer. |
|
Amélioration de opérations du four et réduction des émissions polluantesLa combustion à l'oxygène améliore la flexibilité et la stabilité des opérations du four, et supprime la présence d'azote dans votre four, réduisant ainsi fortement les émissions. En effet, le niveau de NOx est plus de 10 fois inférieur à celui de la combustion à l'air. |
|
Amélioration de la qualité du produit finalEn améliorant la flexibilité et la stabilité des opérations du four, vous améliorez la qualité de ce que vous produisez. |
|
Réduction des dépenses d'investissement (CAPEX)Les équipements permettant de préchauffer de faibles volumes d'oxygène de combustion sont moins coûteux que ceux permettant de préchauffer de plus grands volumes d'air de combustion. |
|
Augmentation de la productivité
|
|
Allongement de la durée de vie de vos installations
|
Nos solutions d'oxycombustion pour l'industrie de la métallurgie
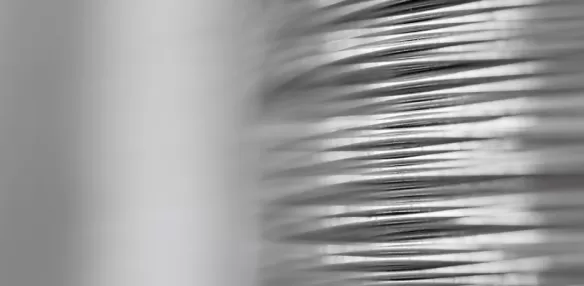
BOOSTAL™ Oxycombustion pour les métaux non ferreux
Professionnels de la fusion primaire de métaux non ferreux, des fonderies, fonderies secondaires et de l'affinage, vous cherchez à réduire les émissions polluantes dans l'atmosphère, réduire votre empreinte carbone et/ou augmenter votre cadence de production ?
Les métaux sont parfois recyclés et contiennent différents niveaux de contamination en termes de composés organiques volatils (COV). Ces métaux sont généralement fondus dans des fours à réverbère et des fours rotatifs équipés de brûleurs régénératifs pour réduire la consommation d'énergie en préchauffant l'air de combustion. La combustion de l'air génère des émissions qui ne permettront pas d'atteindre l'objectif environnemental de neutralité carbone d'ici 2050.
Nous proposons une technologie oxy-combustible qui consiste à injecter de l'oxygène pur au lieu de l'air dans la charge à fondre. Les brûleurs oxy-combustibles améliorent l'efficacité transfert de chaleur, ce qui accélère la fusion et augmente la productivité.
En l'absence d'azote, le volume d'oxygène de combustion est inférieur à celui de l'air de combustion. Cela réduit le besoin en énergie et, par conséquent, les émissions de NOx et de CO2.
BoostAL™ pour les métaux non ferreux vous offre une une alternative bien adaptée et écoresponsable aux brûleurs à air régénératif.
Avantages environnementaux
Jusqu'à 90 % de réduction des émissions de NOx.
Jusqu'à 50% de réduction des émissions de CO2
Jusqu'à 50 % d'économie de carburant.
Avantages opérationnels
Augmentation de la productivité jusqu'à 50%.
Réduction du CapEx pour le traitement des gaz de combustion avec un volume à traiter divisé par 5.
Rendement supérieur en métaux recyclés.
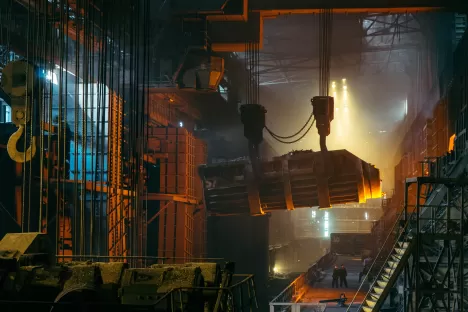
BoostAL™ pour la fusion de la fonte dans les fours rotatifs - Industries de la fonderie et du moulage
Les fours rotatifs sont utilisés pour produire toutes les qualités de fonte grise et de fonte ductile. Historiquement, l'oxygène de l'air de combustion était utilisé pour faire fondre le métal.
Cependant, étant un ballast thermique, l'azote présent dans l'air limite la température de combustion à 900°C.
Lors de la fusion dans un four rotatif, tout le rayonnement thermique accumulé dans le revêtement réfractaire est transmis à la charge métallique avec la rotation du four.
L'utilisation d'oxygène pur augmente la température de la flamme à 1500°C, permettant un transfert d'énergie plus important pour la fusion du métal.
Nous proposons une technologie oxy-combustible qui combine des brûleurs oxy-combustibles et une injection d'oxygène dirigée vers le bain de fusion dans lequel est ajouté un combustible solide (anthracite).
BoostAL™ pour la fusion de la fonte dans les fours rotatifs réduit les émissions atmosphériques, accélère fortement le temps de fusion, augmente la productivité, réduit les coûts d'investissement (unité de filtration plus petite) et améliore le rendement du métal.
Avantages environnementaux
Jusqu'à 90 % d'économie de NOx
Jusqu'à 60% d'économie de CO2 à l'adresse
Jusqu'à 60% d'économie de carburant
Avantages opérationnels
Augmentation de la productivité
Réduction du temps de cycle jusqu'à 30 %.
Réduction des dépenses d'investissement
Volume de gaz de combustion à filtrer divisé par 4
Rendement métallique plus élevé
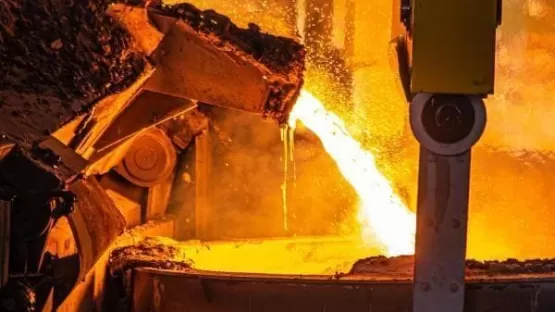
Oxycombustion et ALJET™-CSI pour les cubilots
La solution pour nos clients est la technologie brevetée d'oxy-injection appelée "ALJET™-CSI".
Détails techniques
Dans les fours à cuve et les cubilots alimentés au coke, l'apport d'oxygène technique dans la zone de fusion est à la pointe de la technologie. Il est important que l'oxygène pénètre loin dans le lit de coke et atteigne le centre du four. De cette façon, toute la section transversale du four est utilisée et on obtient une efficacité et une économie élevées du processus de fusion.
Le système ALJET™-CSI atteint les profondeurs de pénétration les plus élevées en injectant l'oxygène directement dans le lit de coke à une vitesse supersonique. En plus de la vitesse supersonique, le système ALJET™-CSI utilise le principe de l'injection minutée. Cela augmente encore la profondeur de pénétration et donc l'efficacité de l'injection d'oxygène. En outre, cela permet d'obtenir la plus grande flexibilité possible du processus du four, puisque la présence de la vitesse supersonique de l'oxygène est garantie dans toutes les conditions de fonctionnement.
Grâce à notre grande expérience dans ce domaine, nous sommes un partenaire expert, nous analyserons volontiers votre processus et prendrons en charge toutes les tâches de la mise en œuvre technique du projet.
Lors de la conception du système ALJET™-CSI, nous accordons une attention particulière à votre processus individuel et aux conditions locales. Par exemple, nous incorporerons, si possible, une technologie de contrôle de l'oxygène déjà existante dans le système ALJET™-CSI, afin de réduire davantage les dépenses d'investissement.
BoostAL™ pour la fusion de la fonte dans les cubilots - Industrie de la fonderie
Fusion de la fonte dans les cubilots
Les cubilots sont des fours verticaux destinés à produire toutes les qualités de fonte grise et de fonte ductile. L'injection d'air par le bas permet de faire brûler le coke solide qui, à son tour, transfère la chaleur à la charge métallique.
Cependant, étant un lest thermique, l'azote présent dans l'air limite la température de combustion à 900°C et les performances du cubilot. Cela limite le taux de productivité, la température de coulée et restreint l'approvisionnement en ferraille.
Pour dépasser ces limites, l'utilisation d'oxygène pur augmente la température de la flamme à 1500°C, permettant un transfert d'énergie plus important pour la fusion du métal.
Nous proposons une offre complète de technologies oxy-combustibles pour différents niveaux d'enrichissement en oxygène qui combinent lances et injection d'oxygène dans les cubilots.
Avec BoostAL™ pour la fusion de la fonte dans les cubilots, trois moyens sont possibles :
- L'enrichissement en oxygène de l'air de combustion qui modifie le gradient thermique dans la zone de combustion en augmentant la.
température maximale. Il est utilisé pour les faibles
enrichissements en oxygène (2 %) de l'air de combustion, sur
toutes les tailles de cubilots.
- L'injection d'oxygène par lances dans la zone de combustion du coke avec des taux d'enrichissement supérieurs à 2% ; L'oxygène est injecté directement dans le cubilot et permet une meilleure pénétration de l'oxygène au centre du cubilot et une meilleure répartition de l'oxygène.
- L'injection d'oxygène par des lances supersoniques pour les cubilots à air chaud pour une pénétration de l'oxygène au centre du centre du cubilot grâce à une vitesse d'injection deux fois d'injection deux fois plus élevée (force momentanée de l'oxygène=230N) que la précédente.
Bénéfices environnementaux
Réduction du coke: jusqu'à 5-10%kg de coke/tonne de fer
Bénéfices opérationnels
- Augmentation de la productivité jusqu'à 7 % à 1 % par % d'enrichissement en oxygène
- Augmentation de la température de coulée jusqu'à 10 °C à +15 °C par % d'enrichissement en oxygène
- Augmentation de la plage de fonctionnement jusqu'à +30% à +50% de la production nominale avec un enrichissement en oxygène de 3%
- Rendement plus élevé de métal
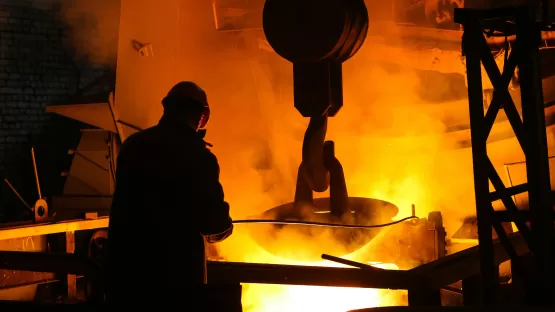
BoostAL™ Oxycombustion pour le préchauffage des poches de transport du métal liquide
Vous cherchez à réduire les émissions polluantes, réduire votre empreinte carbone, ou augmenter votre cadence de production ?
Vous utilisez ou souhaitez utiliser le préchauffage des poches de transport de métal liquide pour minimiser le choc thermique lors de la coulée du métal en fusion , empêcher d'endommager le revêtement réfractaire et/ou réduire les chutes de température du métal dans la poche de coulée?
Ce procédé se fait généralement par combustion d'air tout en étant limité à une température maximale du métal de 1000°C et en étant très gourmand en carburant.
BoostAL™ Ladle Heating est l'offre complète d'Air Liquide pour le préchauffage des poches dans les aciéries et les fonderies.
Nous proposons une technologie avancée d'oxy-combustion qui, grâce à une forte combustion radiative oxygène/combustible
- accélère le chauffage de la surface réfractaire jusqu'à 4x, à une température (définie par le client) qui évite la surchauffe du métal à la sortie du four,
- nettoie en même temps les poches des oxydes accumulés sur la surface réfractaire, et améliore la qualité du métal en éliminant la stratification thermique dans les poches,
- augmente la durée de vie du revêtement réfractaire,
- réduit drastiquement, en éliminant l'azote, la formation de NOX,
- réduit les émissions de CO2 jusqu'à -60% et la consommation de carburant jusqu'à -40%