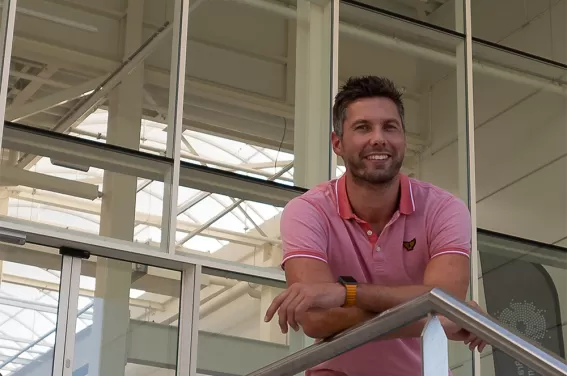
K3D: Metal printing met internationale allure
14/11/2022
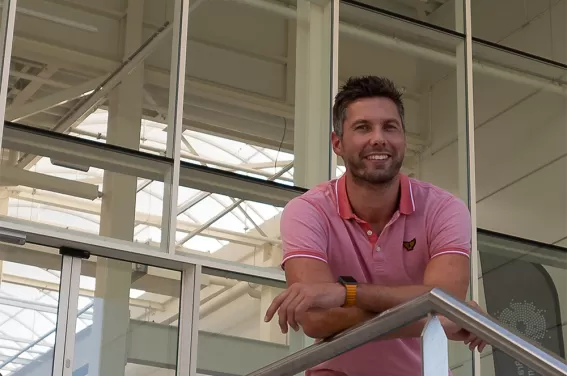
“Air Liquide is een solide partner met een sterk aanbod aan bijkomende diensten”
K3D – met vestigingen in Terborg en Eindhoven – is in Nederland marktleider op vlak van 3D metal printing. In minder dan tien jaar heeft het bedrijf al ruim 150.000 metalen onderdelen geprint die vandaag volop gebruikt worden in allerhande industriële installaties.
K3D is initieel ontstaan als de 3D printafdeling van moederbedrijf Royal Kaak, maar sinds 2018 opereert K3D onder eigen vlag. Royal Kaak is wereldwijd actief als producent van geautomatiseerde bakkerijlijnen en aanverwante producten en diensten. In 2016 investeert Royal Kaak in een hoogwaardige 3D metaalprinter.
“Het was de bedoeling om op die manier snel en efficiënt hoogwaardige reserve-onderdelen te kunnen produceren voor het wereldwijde klantennetwerk van Royal Kaak”, verduidelijkt K3D’s CEO Luuk Wissink. “Want als er iets stuk gaat in een productielijn in, pakweg, Australië kan het niet de bedoeling zijn dat vervangende onderdelen wekenlang onderweg zijn. Door lokaal geschikte 3D metaalprinters te voorzien kan dat probleem worden opgelost.”
10% voor Royal Kaak, 90% voor eigen klanten
En die aanpak werkt prima. Alleen bleek dat de productiecapaciteit van de machine vele malen hoger ligt dan wat nodig is om de vervangende onderdelen te kunnen produceren. En dus werd gezocht naar een methode om de resterende productiecapaciteit van de ruim € 2 miljoen kostende machine nuttig in te vullen.
Royal Kaak besloot daarop om de 3D printing activiteiten in een aparte entiteit onder te brengen en er een op zichzelf staand stabiel en winstgevend bedrijf van te maken. En dat is gelukt. K3D produceert enerzijds zelf 3D prints voor haar klantenbestand – 10% van de productie is bestemd voor Royal Kaak, de rest voor overige klanten — en stelt anderzijds de machine ter beschikking aan enkele externe partijen, waarbij elke partij een deel van de machine betaalt.
One stop shop
“K3D is een one stop shop voor 3D metaalprinting. Indien gewenst zorgen we ook voor het design van het te printen stuk en gaan we met onze klanten in dialoog om na te gaan wat ze precies nodig hebben, zodat we hun vraag op de best mogelijke manier te kunnen invullen.”
“We hebben drie Additive Industries MetalFAB1 printers ter beschikking – twee in Terborg en één in Eindhoven – en zorgen indien nodig ook voor het nabewerken van de geprinte stukken. Eenvoudige nabewerkingen, zoals trommelen, slijpen en stralen doen we in eigen huis, terwijl we beroep doen op andere partijen binnen ons ecosysteem voor meer complexe nabewerkingen, zoals draaien en frezen.”
Unieke expertise dankzij voortdurende research
K3D heeft een benijdenswaardige reputatie opgebouwd en staat inmiddels bekend als één van de beste 3D metaalprinting bedrijven in West-Europa. “Natuurlijk zijn we heel tevreden met die reputatie. Naar ons idee heeft dat enerzijds te maken met onze algehele kwaliteitszorg – met daarin een belangrijke rol voor onze MetalFAB1 machines van Additive Industries – en anderzijds met onze ervaring.”
“Intussen hebben we namelijk al heel wat opdrachten achter de rug waar we bijkomende research voor hebben moeten uitvoeren, en op die manier bouwen we flink wat bijkomende expertise op die we telkens meenemen naar onze volgende opdrachten.”
Extra robots beschikbaar
Het klantenbestand van K3D strekt zich uit over heel wat verschillende sectoren: automotive, bouw, energie, hightech, kunst, lucht- en ruimtevaart, offshore, robotica, tooling en onderdelen voor de traditionele machinebouw. “We hebben intussen al meer dan 150.000 stukken mogen printen, en dat voor de meest uiteenlopende toepassingen: van onderdelen voor robots in voedselproductielijnen tot prints voor de vliegtuigindustrie, oplossingen voor offshore toepassingen, en ga zo maar door.”
“Dikwijls komt de klant zelf met een ontwerp naar ons. We geven daar dan feedback op, wat vaak resulteert in een beter eindresultaat. Het komt ook voor dat de klant met een fysiek onderdeel komt, dat wij dan scannen en reverse engineeren.”
En dat leidt wel eens tot bijzondere resultaten. Zo heeft K3D een onderdeel geprint dat aan het eind van een robotarm moet worden gebruikt en dat maar liefst 90% lichter is dan het originele onderdeel. Dankzij die significante gewichtsbesparing kan de robot sneller functioneren waardoor de productielijn nog slechts zes robots nodig heeft, terwijl er voorheen acht stuks nodig waren. Het spreekt vanzelf dat daar een aanzienlijke kostenbesparing mee gemoeid is. Daarbij kan het onderdeel sneller gereinigd worden, zodat ook de downtime afgenomen is.
Air Liquide als toegevoegde waarde
“In Eindhoven bevindt onze vestiging zich op een grote site (Brainport Industries Campus, n.v.d.r.), samen met heel wat andere bedrijven uit de hightech maakindustrie. Daarom moest onze argon gastank op een flinke afstand geplaatst worden en was er een leiding van maar liefst 120 meter nodig om het argongas tot bij onze machine te krijgen.”
“De gehele gasinstallatie is aangelegd in nauwe samenwerking met Air Liquide. Eén van de redenen waarom we met Air Liquide in zee gegaan zijn is dat ze een bevoorrecht partner zijn van Additive Industries. Daardoor wisten we zeker dat de gassen van Air Liquide uitstekend kunnen gecombineerd worden met onze MetalFAB1 printers.”
“Intussen heeft Air Liquide zich een solide partner getoond met een grote leveringszekerheid en met een sterk aanbod aan bijkomende diensten. Zo heeft Air Liquide nu ook een telemetriesysteem geïnstalleerd op onze argontank waarmee we zelf kunnen inloggen via het MyGas portaal en zo ons verbruik kunnen monitoren.”
Meer printen met minder materiaal
“Voor ons is het duidelijk dat metaalprinten een grootse toekomst tegemoet gaat”, stelt Luuk Wissink. “De levertijd voor een te printen onderdeel bedraagt niet meer dan tien werkdagen, wat beduidend minder is dan de leveringstermijnen van traditioneel geproduceerde onderdelen. Daarbij is het ook qua materiaalgebruik een stap vooruit. We gebruiken precies de hoeveelheid metaalpoeder die nodig is om het onderdeel te maken. Van enige verspilling is dus geen sprake.”
K3D is er alleszins helemaal klaar voor. Sinds kort heeft het bedrijf twee nieuwe laser metal deposition printers in gebruik genomen die stukken tot wel 3 x 3 x 3 meter kunnen printen.
Het gaat om een Meltio M 450 desktopprinter en een Meltio Engine robotkop. De Meltio Engine versmelt metaaldraad tot vloeibaar metaal om zo het eindproduct laag op laag aan elkaar te lassen. Dankzij deze techniek kunnen diverse staalsoorten (roestvrijstaal 316L en 308L, zacht staal ER70S, alsook titanium en nikkel) met een fijne oppervlaktestructuur in grote formaten worden geproduceerd.
Wil je meer weten over onze oplossingen voor additive manufacturing & 3D printing?
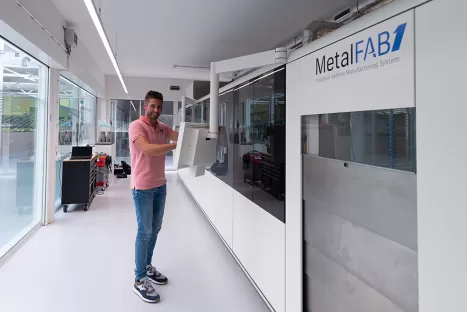